The Ultimate Guide to Screw Compressors – Efficiency, Applications, and Benefits
In the world of industrial machinery, screw compressors have emerged as one of the most reliable and efficient solutions for businesses across various sectors. Their design, operational efficiency, and versatility make them a top choice for industries ranging from manufacturing and construction to automotive and food processing.
In this comprehensive guide, we’ll dive deep into what makes screw compressors unique, their applications, benefits, and how to choose the right one for your needs.
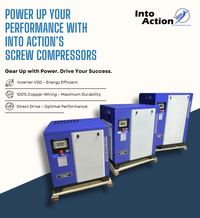
What Are Screw Compressors?
Screw compressors use two intermeshing helical rotors to compress air or gas. As these rotors turn, the air is trapped between them, reducing its volume and increasing pressure. This continuous, smooth operation makes screw compressors more efficient than traditional piston-based models, especially for large-scale industrial applications.
Types of Screw Compressors
1. Oil-Injected Screw Compressors:
• Use oil for lubrication, sealing, and cooling.
• Ideal for heavy-duty industrial applications like metal fabrication and automotive manufacturing.
2. Oil-Free Screw Compressors:
• No oil is used in the compression chamber, ensuring contaminant-free air.
• Perfect for industries requiring high air purity, such as pharmaceuticals, food processing, and electronics.
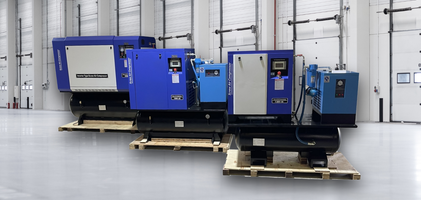
Key Advantages of Screw Compressors
1. High Efficiency and Continuous Operation
Screw compressors can run continuously without overheating, making them ideal for operations that require a steady, reliable air supply.
2. Lower Maintenance Requirements
Fewer moving parts mean less wear and tear, reducing maintenance costs and extending the compressor’s lifespan.
3. Quiet Operation
Compared to piston compressors, screw compressors operate more quietly, making them suitable for indoor environments where noise reduction...
4. Energy Efficiency
Variable Speed Drive (VSD) technology allows screw compressors to adjust their motor speed based on air demand, reducing energy consumption...
Choosing the Right Screw Compressor
Airflow Capacity (CFM – Cubic Feet per Minute)
The airflow capacity determines how much air the compressor can deliver. This is measured in CFM and indicates whether the compressor can handle your equipment’s air demand.
• Low CFM (under 50): Suitable for light-duty tasks such as small pneumatic tools or low-volume production lines.
• Medium CFM (50–250): Ideal for mid-sized operations, including automotive shops and packaging systems.
• High CFM (250+): Designed for large-scale industrial applications, such as manufacturing plants, construction sites, and mining operations.
Tip: Calculate your total air demand by adding up the CFM requirements of all connected tools and machines, then choose a compressor with at least 20% more capacity to accommodate future growth or unexpected spikes.
Pressure Requirements (PSI – Pounds per Square Inch)
The PSI rating reflects the pressure the compressor can generate. Different industries and tools require varying pressure levels:
• Low Pressure (90–125 PSI): Suitable for general-purpose applications like automotive repair and assembly lines.
• Medium Pressure (125–175 PSI): Ideal for processes like sandblasting, spray painting, and packaging.
• High Pressure (175+ PSI): Necessary for heavy-duty industries like mining, aerospace, and oil refining.
Tip: Always check the PSI requirements of your tools and ensure the compressor can consistently meet or exceed these demands.
Oil-Injected vs. Oil-Free Screw Compressors
Choosing between oil-injected and oil-free screw compressors depends on your industry’s specific needs:
1. Oil-Injected Screw Compressors:
• Offer better cooling and sealing, resulting in higher efficiency.
Suitable for heavy-duty applications like metal fabrication, automotive, and construction.
• Require regular maintenance to change oil and filters, which can add to operational costs.
2. Oil-Free Screw Compressors:
• Provide clean, contaminant-free air, essential for industries like food processing, pharmaceuticals, electronics, and healthcare.
• Lower maintenance costs due to the absence of oil, but initial costs may be higher.
Tip: If your operations involve sensitive products or processes requiring ultra-clean air, go for oil-free compressors despite the higher upfront cost.
Power Source: Electric vs. Diesel
1. Electric Screw Compressors:
• Best for indoor use, where electrical infrastructure is readily available.
• Quieter, more energy-efficient, and environmentally friendly.
• Lower operational costs in facilities with steady power supply.
2. Diesel Screw Compressors:
• Suitable for outdoor, remote, or off-grid applications like construction sites and mining operations.
• Provide higher mobility and independence from power grids but require regular refueling and emit more noise and exhaust.
Tip: Consider the location and power availability of your site when deciding between electric and diesel models.